How to save money on your next set of patent drawings
The type of reference material you supply your draftsperson directly influences the price you pay for patent drawings. Reference material comes in many forms and the better you are at identifying the most useful reference materials, the less you will pay for drawings. It’s not complicated and with the following tips I hope you will save money on your next set of patent drawings.
The most cost effective method for creating patent drawings is to make drawings from engineering Computer Aided Design and Drafting (CAD) files. Most patent drafters are skilled in CAD. By using existing CAD files a draftsperson does not need to recreate the drawings from scratch. If an item has already been manufactured or a prototype built, chances are there are existing CAD files, used in almost all modern manufacturing processes.
CAD programs are used in many applications, including automotive, shipbuilding, aerospace industries, industrial and architectural design, prosthetics and many more. Some of the more frequently used CAD programs areAutoCAD, Mechanical Desktop, Inventor Series, SolidWorks and Pro/Engineer. There are many CAD file formats, some of which are DWG, IGES, STEP, STL, SAT(ACIS). These names are acronyms that usually serve as the file extension.
In your quest to get the best CAD files, ask for “source files” or original CAD files (files that the original manufacturing drawings were created in). CAD files come in a 3D or 2D form. In 3D or 3 dimensional files, all dimensions for every surface are encoded into the solid model. From the 3D solid model, your draftsperson is able to compute 2D views, e.g. front, back, left, right, top and bottom. Additionally a perspective view can be rotated to the desirable orientation and projected. The projections are 100% accurate even on the most complicated assemblies or components. If a case has already been filed and 3D files are available please make sure they are the same version as filed. If 2D files are supplied please ensure that they are the same parts and views as filed.
Unless you have CAD software, you will not be able to open or view CAD files. Very often, engineers/inventors will send viewer files. These are a version of the original CAD files which enable you to view CAD files without owning the software; EASM files for SolidWorks, DWF for AutoCAD and so on. While you can view this type of file, it is not helpful to your draftsperson because it cannot be edited or manipulated.
If you have CAD files that you cannot view, you can download viewer software (usually free) from the software producer or send the original CAD files to your draftsperson and have them supply you a PDF version of those.
Not all reference materials originate in a CAD platform. For images created in programs other than CAD, ask for original source or native file (files in the program they were created in), which can in many instances be edited. Some more common programs that generate editable files are CorelDRAW, Visio, Adobe Illustrator and PowerPoint. Raster Files are un-editable and used for reference only, these include JPEG, TIFF, GIF some EPS and some PDF.
When photographs or slides are used, send full color digital versions (often in JPG or PDF format) to your draftsperson. Images or photographs inserted into PowerPoint presentations or word documents are not first generation. If you have a marked up image with numbering or labels, scanned copied or inserted it’s a second or third generation image. With each generation, quality is lost and with quality loss, details vanish. Converting full color images into black & white copies creates a whole set of new problems for your draftsperson. Think of it this way, if you have a full color image, each element may be defined by a specific color. If you have a blue item next to a red item of the same density, converted to black & white they will become the same shade of black and you lose definition between the two.
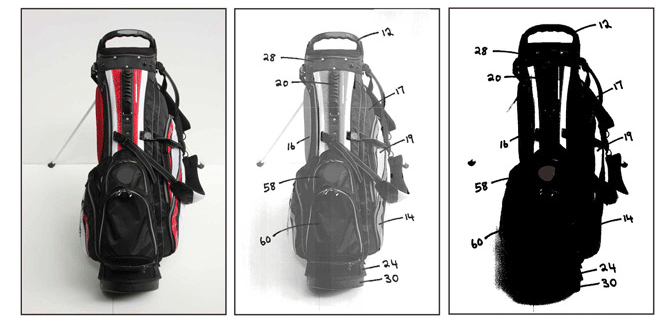
(2) Scanned, using grayscale setting – loss of detail has occurred;
(3) Scanned, using Black & white setting – all detail is lost
A solution is to send marked up and original unmarked images, so that your draftsperson can use the marked up versions for numbering & labels and the unmarked version for details.
If you send only the marked up version, your draftsperson will spend more time trying to decipher the elements/details of the image, and more time equals more cost.
When taking photographs of an item, the following recommendations will help to get the most useful photographs. Specific views are especially important if you are using these as reference to create drawings for a design application.
Taking the photographs to depict the exact views can be tricky in itself. For instance, the invention should stay in exactly the same position for all the photographs and the camera should move around the invention at the same height and distance. Also the photograph should show only the side of the invention that is relevant. If you are photographing a cube; for the side view, the photograph should be taken in a way that shows only the side and not the side and a bit of the top. This method should apply to all the views. Take as many photographs as you can in this manner, your draftsperson will select the ones that are useful.
Additionally a top and a bottom view is needed For the best results take the top view from directly above the item and the bottom directly from below if possible.
Since photographs distort perspective a certain amount of correcting will be necessary. Drawings made from poor photographs need more correcting, take longer and cost more. Make sure that the photographs you send are in focus. You would be amazed at how many fuzzy, blurry photographs we receive.
Remember the worse the image, the longer it takes your draftsperson to decipher the details.
Since we are not able to judge depth from photographs, generally a sketch with dimensions is usually very helpful. There is a simple method used to determine the scale of objects in photographs. If you are photographing a small object, Place a ruler next to it so that we can see the length of the object. For larger objects please provide a scale or legend.
Conclusion
When meeting with your client get the best reference materials available. If reference materials are so poor that you cannot see details, your draftsperson cannot see them either. The bottom line is, the more time your draftsperson spends trying to figure out details the higher your cost will be for drawings.
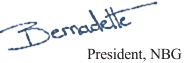